The
rotary drum granulator passes a certain amount of water or steam to make the basic fertilizer fully chemically react in the cylinder after the humidity is adjusted. Under a certain liquid phase condition, with the help of the rotation of the cylinder, the material particles can be squeezed and agglomerated. Into a ball. The important principle of the drum granulator to produce compound fertilizer is to minimize the addition of water during granulation, and to moderately increase the temperature and solubility of the material, so as to reduce heat energy consumption, increase the qualified rate of pellets, increase output, and reduce production costs.
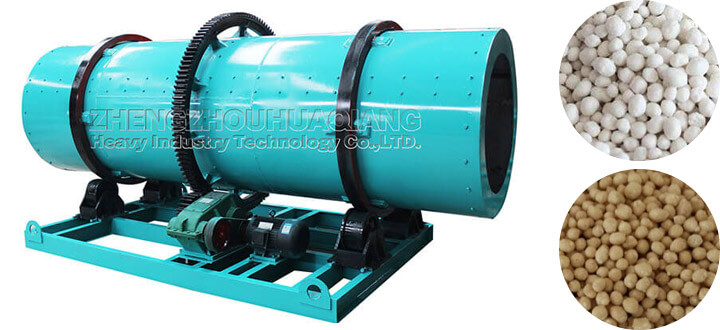
The agglomeration granulation method of the rotary drum granulator means that the powdery particles agglomerate together to form micronuclei under the action of liquid bridge and capillary force during the granulation process. The agglomerated micronuclei are friction and rolling caused by the low-speed rotation of the container. Under the action of impact force, the it continuously rotates and grows in the powder layer, and finally becomes spherical particles of a certain size. In the case where the particle shape is desired to be spherical and the particle density is not high, the mode of agglomeration granulation is mostly chosen.
The characteristics of agglomeration granulation by rotary drum granulator:
1. The material can be granulated when the moisture content is between 30% and 40%, and the output moisture content is about 30%. This reduces the drying requirements of the traditional 70% moisture process and effectively reduces the production cost of organic fertilizer.
2. During the granulation process of
fertilizer granulation machine, a temperature of 50-65 degrees is generated in the cylinder, which reduces the moisture content of the discharged particles by 5-8 points, thereby reducing the drying cost requirements.
3. The granulated particles are uniform, smooth, round, and high-strength, and the particle forming rate is more than 95%.
4. Adjust the size of the output particles by adjusting the water content of the feed, and then meet the requirements of different particle sizes.