Common organic fertilizer granulators on the market include: roller extrusion granulator, rotary drum granulator, disc granulator machine, new organic fertilizer granulator, new two-in-one organic fertilizer granulator, flat die Granulator, ring die granulator, today we will take you into the double-roll granulator.
The double roller granulator, this equipment can directly compress and granulate powdery materials with water content mellow and less than 5% in the granulation process, and one-time molding, the product can be directly packaged by organic fertilizer packaging machine equipment. It avoids the drying and cooling process after granulation in the traditional organic fertilizer production process. So, how to install and debug the newly purchased dry roll granulator? The working principle of the dry roll granulator is that the material is forced to be compressed into small pieces through the gap between two relatively rotating rolls through external pressure. During the rolling process, the actual density of the material can be increased by 1.5 to 3 times to meet the requirements of the fixed particle strength.
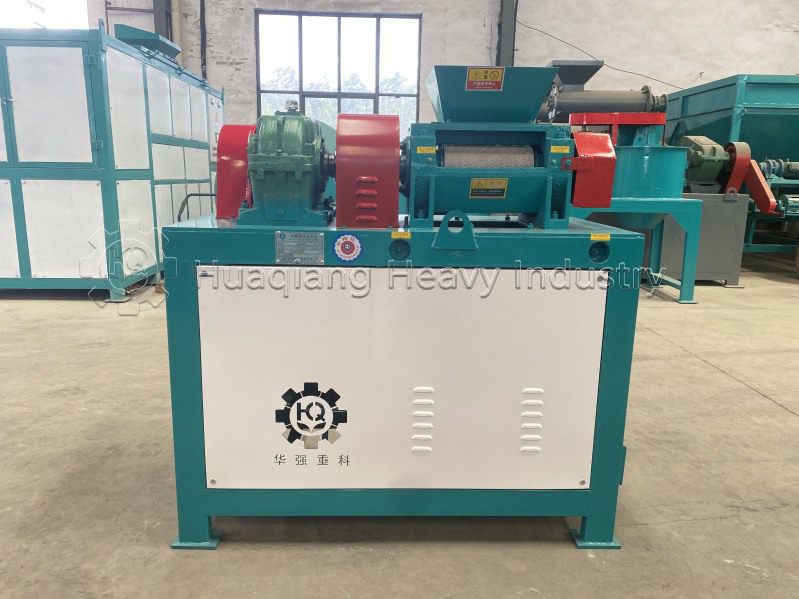
Double roller granulator is granulation equipment, which can be used in organic fertilizer production line, npk fertilizer production line and so on. No waste discharge, stable operation, reliable operation and convenient maintenance. Wide adaptability of raw materials, suitable for granulation of compound fertilizers, pharmaceuticals, chemicals, feed and other raw materials.
The roller extrusion organic fertilizer granulator is an improved product that absorbs the new technology of the international granulator. The machine is equipped with a feeding system connected with a pre-feeder and a forced-feeding screw feeding hopper that is assembled with the machine to ensure the continuity, richness and symmetry of the feeding, which is a crucial step. Uniform arc grooves are engraved on the paired rollers, which is conducive to material biting into the rollers, resulting in arc grooves sealing the cavity (belt), and also conducive to material compaction, reducing the forming pressure of the mechanism and the load of the main machine, and improving the manufacturing rate of the rollers.